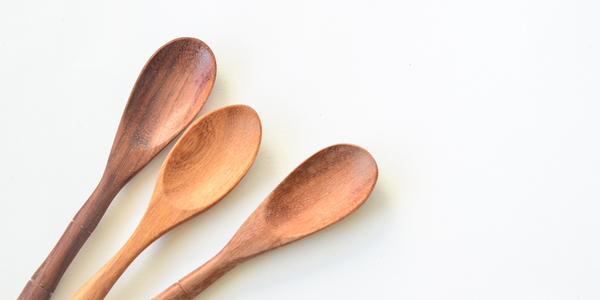
- Analytics & Modeling - Machine Learning
- Food & Beverage
- Business Operation
- Advanced Production Planning and Scheduling
- System Integration
Magic Spoon
Magic Spoon produces cereal for grown-ups that still reminds them of their favorite flavors from childhood. Their formulas are high in protein, low in carbs, and magically tasty. The team produces all of its cereals with suppliers in the United States and sells its products directly to consumers and through e-commerce sites and retailers.
After a year of managing their supply chain using Google Spreadsheets for production, DEAR Systems for inventory and demand planning, and a variety of freight forwarders for shipments, all of their data was in separate places. They did not have up-to-date information from their suppliers in their systems, and therefore, were bogged down in fixing discrepancies using a manual workflow that didn’t allow them enough time to plan for production delays.
- Founded in April 2019
- Based in New York, NY
- Food and Beverage industry
- $5+ million in annual revenue
- Simplify their supply chain workflow
- Increase communication with suppliers
- More time to fix data discrepancies
- Advance notice when delays were expected
Magic Spoon selected Anvyl to help them increase collaboration and communication with suppliers, reduce manual workflows and data discrepancies, and get alerts for potential production delays.
As the team had more free time, they were able to leverage Anvyl IQ’s machine learning tools that helped them predict the likelihood of a production delay.
Case Study missing?
Start adding your own!
Register with your work email and create a new case study profile for your business.
Related Case Studies.
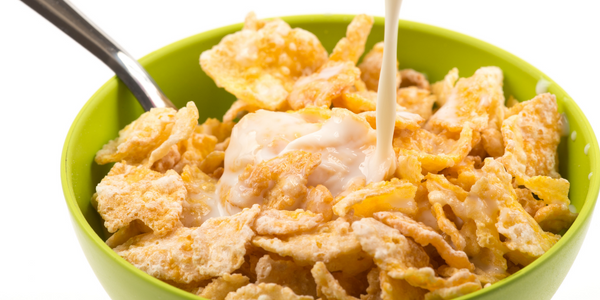
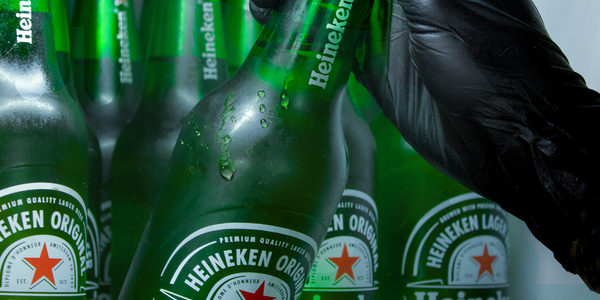
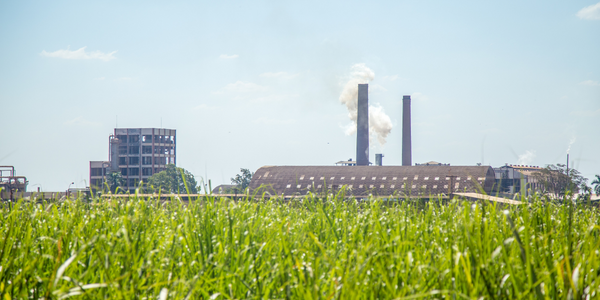
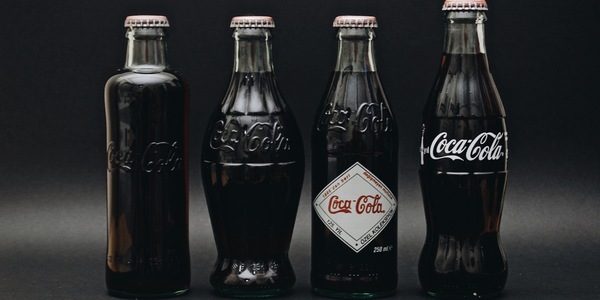
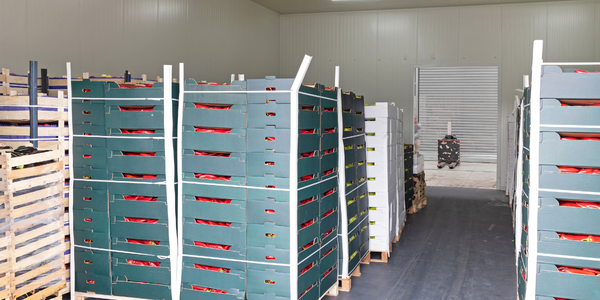
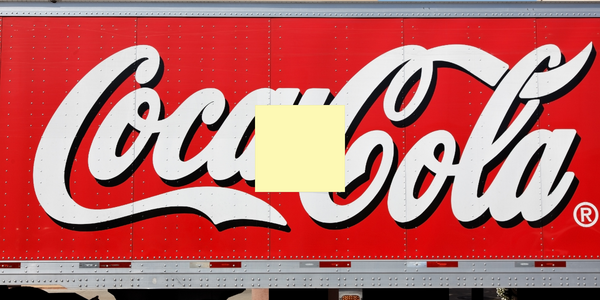