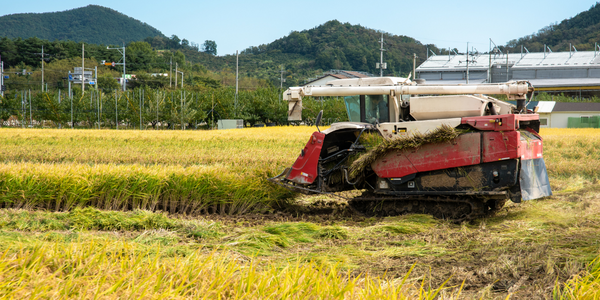
- Functional Applications - Remote Monitoring & Control Systems
- Infrastructure as a Service (IaaS)
- Agriculture
Delivering a high-performance, automated turf harvester that reliably and efficiently palletizes turf in a variety of farming conditions while increasing farm productivity, reducing machine operating costs, and providing a secure Internet gateway to remotely monitor and control the turf harvester.
Using LabVIEW software and CompactRIO hardware to design the ProSlab 155, a smart machine harvests turf 20 percent faster, and uses half the diesel fuel than other turf harvesting machines on the market. Traditional Approach Hand-stacked turf harvesting is still widely used in the industry. Farm equipment companies have tried to build machines to automate turf slab cutting and stacking over the years to improve productivity, but the machines’ traditional approach makes them either perform inconsistently or increase productivity only slightly more than the hand-stacking process. They incorporate common mobile equipment such as electrically operated valves that control fluid power to hydraulic cylinders and motors for motion control. Though reliable for simpler systems, these components have been less effective for performing many parallel operations in tight synchronization with other processes as well as implementing the complex math needed for advanced signal processing and high-speed motion control trajectory generation. In addition, limited data processing power and closed system architectures limit advanced functionality and remote monitoring and diagnostics. The FireFly Approach Recognizing these shortcomings, we worked to build a smarter machine that manages and synchronizes multiple parallel processes to automate cutting and stacking turf grass. First, a cutter lifts the turf from the ground and cuts it into slabs that conveyors transport to the rear of the machine. A stacker attached to a gantry then moves the cut slabs from the conveyors to the pallet. As each turf slab is stacked onto the pallet, a set of pallet forks lowers the pallet of turf closer to the ground. Once stacked to the desired level, the fully loaded pallet of neatly stacked turf slabs is placed on the ground as a pallet magazine holding empty pallets inserts a new, empty pallet onto the pallet forklift, enabling the cutting and stacking process to continue uninterrupted. A self-propelled tractor moves the entire automated system through the field. These systems must work in a continuous, synchronized flow for the machine to reliably and efficiently perform the work of harvesting and stacking the turf. In total, the machine includes nearly 80 analog and digital sensors and 100 digital outputs. We incorporated servo electric systems with coordinated multiaxis trajectory generators to provide the high-speed, efficient, accurate, and smooth motion control necessary for the complex stacking process. The machine can consistently stack turf slabs over millions of cycles per year, which improves speed and reliability greatly. We chose traditional fluid power systems for the less complex tasks of the harvester including operating the cutter, fork lift, pallet magazine, and propulsion systems. To facilitate future development, we required an open, flexible and powerful platform for designing, prototyping, and ultimately deploying its new machine around the world. LabVIEW RIO Architecture Using the LabVIEW and CompactRIO platform, we combined traditional fluid power systems with servo electric systems on a machine to perform many complex parallel operations. CompactRIO’s modular I/O enables users to flexibly implement a wide array of sensor types and industrial connectivity. The CompactRIO real-time controller and reconfigurable FPGA chassis provide a customizable platform to implement complex, highly synchronized control systems. LabVIEW’s inherent ability to implement many parallel loops on the FPGA and real-time controller, its rich set of complex math functions, and its integration with the LabVIEW SoftMotion Module and Kollmorgen AKD drives and motors make it powerful software to control all aspects of a smart machine. Additionally, the open and flexible nature of LabVIEW helps implement reliable communication architectures for local operator interfaces and centralized resource management, diagnostics, and remote updates. These functions are essential once the machines are deployed around the world and need maintenance.
Case Study missing?
Start adding your own!
Register with your work email and create a new case study profile for your business.
Related Case Studies.
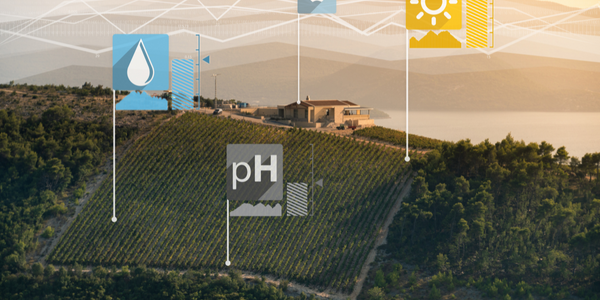
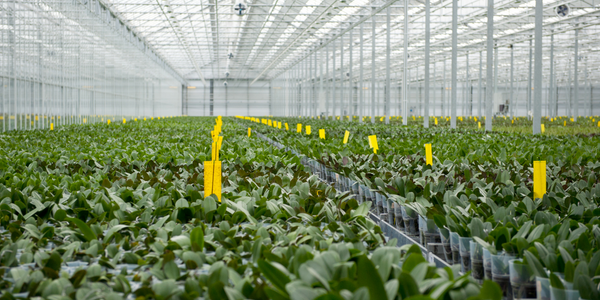
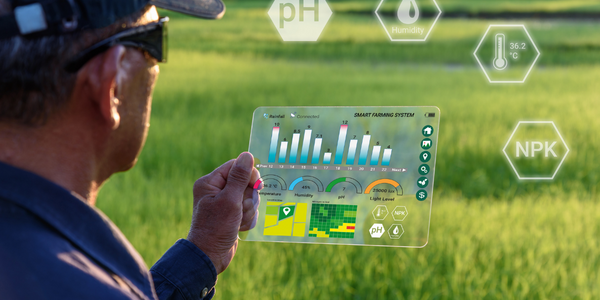
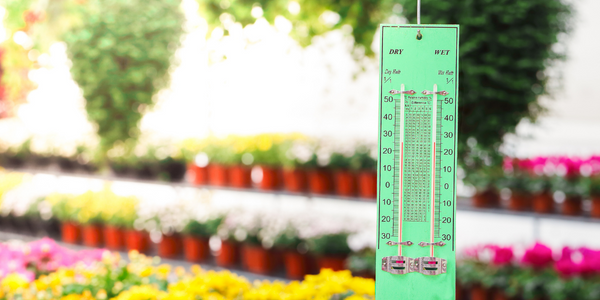